AlSiC作为封装材料的基本特点有哪些?
发布时间:2022-06-24 浏览次数:411次
一、AlSiC作为封装材料的基本特点
(1)热膨胀系数低(可调节):与Si、GaAs、AlN等无机陶瓷基片材料热匹配良好;
(2)热导率高:大大高于Kovar合金,可有效地扩散大功率芯片产生的热量;
(3)密度小:密度大大低于W/Cu、Mo/Cu和Kovar合金,可有效减重;
(4)比强度和比模量高: 比模量是Kovar和W/Cu的4倍、Mo/Cu的2倍;
(5)AlSiC-铝基碳化硅材料轻质、热膨胀系数可调匹配、热导率高、价格适中。
按照不同的增强体,铝基复合材料分为纤维增强和颗粒(直径在0.5——100μm之间的等轴晶粒)增强、晶须增强铝基复合材料。常用的增强颗粒主要包括SiC、Si3N4、Al2O3、TiC、TiB2、A1N、B4C以及石墨颗粒或者金属颗粒等。
常见的几种铝基复合材料的制备工艺有粉末冶金法、压力浸渗工艺、反应自生成法、高能高速固结工艺、半固态搅拌复合制造、喷射沉积法、搅拌摩擦加工法及球磨法制备纳米碳管增强铝基复合材料等。TiB2/A1复合材料的制备方法较多,主要有喷射沉积法、LSM、XDTM、挤压铸造、接触反应法、自蔓延高温合成法和反应机械合金化及粉末冶金法等。常见的方法有原位生成法、粉末冶金法、机械搅拌法、挤压铸造法、喷射沉积法、浸渗法等,下面主要对这六种方法进行介绍。
原位生成法
原位生成法由Koczak 等人于 1989 年首次提出,其原理为按照材料预先设计的需求选取合适的反应剂,然后在特定的环境下将温度升到能使原料内特定元素发生物理化学反应的温度,在这样的条件下材料内部能够反应生成一种或几种均匀分布在基体内部的且热力学稳定的增强体材料,以达到强化的效果。
原位内生法的优点在于原位生成的增强体颗粒在基体内分布均匀,二者之间的界面干净无污染、工艺简单等,故而该方法具备广阔的应用前景,经近几十年的发展,已细化完善出了许多不同的制备工艺,比如:自蔓延高温合成法、弥散放热法、熔盐辅助法和直接反应法等。但是该方法也有一定的缺点,对于制备复合材料的原材料有一定要求,需要满足一些反应条件同时反应的副产物的生成难以控制,另外还存在界面问题等。
粉末冶金法
粉末冶金工艺是最常采用的且最早用于制备纳米颗粒增强铝基复合材料的工艺之一。其制备过程是:先将陶瓷颗粒增强体与铝合金基体粉末在球磨罐中均匀混合,混合过程既可以干混也可以在液体环境下进行。混合后的粉体经过冷压成坯、真空排气、热压烧结及后续处理(如挤压、轧制、热处理等)制得所需的复合材料。
粉末冶金工艺制备过程一般在真空或保护气氛防护下进行且烧结温度低于铝合金的熔点,从而大大的降低了发生界面反应的可能性。粉末冶金法制备铝基复合材料可以大范围调控陶瓷颗粒的尺寸和含量,而且可以保证纳米颗粒增强体在基体中较均匀的分布,减少团聚与偏析的出现,从而使复合材料得到增强。
该方法的缺点则在于材料容易出现气孔,致密度不高。因此,必须通过挤压、轧制或热处理等工艺进行二次处理以改善其致密度及机械性能。此外,粉末冶金制备工艺比较繁琐,通常需要密封、真空或者保护气氛的工作条件,而且烧结温度选择不当会导致偏析。
机械搅拌法
机械搅拌法是在搅拌的过程中将增强体颗粒加入到基体金属液中,利用高速旋转的搅拌装置使增强体均匀混合入基体金属液之中,然后浇入模具中得到想要的铸件。其生产设备见图2所示。机械搅拌法操作过程较为简单,成本低廉,不到其他加工工艺的一半,是可以广泛应用的方法,目前工业上制备复合材料大多数都是采用该方法。
综合国内外对搅拌铸造的研究发现,搅拌铸造法可以以搅拌时的熔体温度为依据,将其分为液态搅拌和液半固态搅拌两种方法。液态搅拌法主要是使搅拌温度保持在液相线以上,一边搅拌一边加入增强体颗粒,搅拌之后可以直接进行浇铸。半固态搅拌是指将搅拌温度调制固液相线之间,使熔体之中有一定的固相体积分数。这样在搅拌的时候熔体中会有更大的剪切力容易使增强体颗粒分布均匀。
这两种方法各有优缺点,液态法简单,但是卷气很严重,颗粒分散的不够均匀。但是半固态搅拌铸造法目前仍存在一些问题,如在搅拌过程中陶瓷颗粒容易产生偏聚、界面处易发生反应等。其次,在空气环境下进行搅拌时,搅拌的过程中尤其是高速搅拌时很容易吸入气体,使得最后浇铸出的复合材料产品内部出现有害的气孔缺陷。再次,颗粒增强相添加的体积分数有一定限制是利用搅拌铸造法制备金属基复合材料的另一个问题。
挤压铸造法
这种方法首先是要按照零件的形状将增强体材料制备成预制块,然后放入铸型。在重力下浇注液态金属或合金,随后对金属液施加压力,使基体熔液渗入到预制块中形成锭。
挤压铸造后得到的材料均匀性非常良好,材料内部没有明显的缺陷。这是因为碳化硅颗粒与铝合金基体的结合界面非常好,结合的十分紧密,使得二者之间的界面能够起到传递载荷的作用,实现抑制铝基体的膨胀的情况。
挤压铸造法还有诸多优点:制备出的产品尺寸准确稳定,省去了后期二次加工的麻烦;金属液浸渗的时间很短,因此能够获得很快的冷却速度,这样可以大大减少不良界面反应的发生;加入增强相的量可以自由的调节其范围。但是该方法工艺复杂,不利于用来成型形状复杂的产品,而且如果使用浸渗的压力比较大,可能会对产品形状和模具的完好性产生很大的影响。
喷射沉积法
喷射沉积法是一种新型的加工工艺,主要是将熔化的基体金属液在高速流动的惰性气体中雾化向外喷出,同时将增强体颗粒添加到雾化喷出的金属液体中,使两者在沉降的过程中混合,最后共同在经过预处理的基体上沉积制得想要的复合材料。
这种方法的优点是可以随意调节增强体相的体积分数,而且增强体材料的粒度大小在制备时也不受限制。得益于增强体颗粒与基体熔液之间接触的时间很短暂,因此二者之间反应时间非常有限,这样可以明显的改善二者之间的界面的结合状态。因此雾化沉积技术可以使得基体保持快速凝固的特点,得到的晶粒十分细小。
浸渗法
浸渗法通常有两种主要形式,包括无压浸渗和压力浸渗。无压浸渗相对简单,就是将基体Al合金在可控气氛炉中加热,使其超过液相线温度;然后在不加压力的条件下,使合金溶液自行浸渗到SiC预制体中去的制备方法。压力浸渗的区别就是加上压力条件,其方法接近于挤压渗透铸造。
浸渗法是一种成本较低且工艺简单的制备技术。因而常用于高体积分数SiCp/Al基复合材料的制备,制得的材料SiC颗分布相对均匀。成熟的无压浸渗法制备的SiC/Al复合材料材料甚至已经能够应用于电子封装。但这种方法对预制体引入的高孔隙率难以控制。
以上就是本篇“AlSiC作为封装材料的基本特点有哪些?”的全部内容,想要了解更多,请持续关注本站。
28
2022.03
半导体材料发展前景
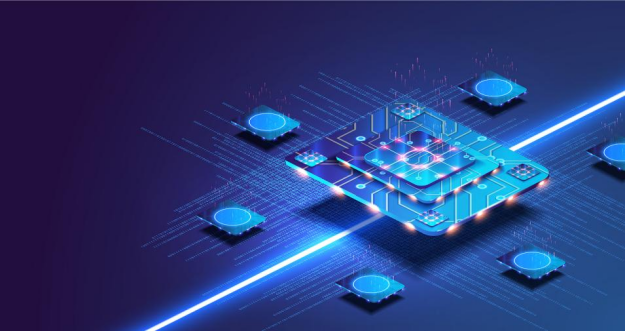
随着物联网、大数据和人工智能驱动的新计算时代的发展,对半导体器件的需求日益增长,同时也催生了市场对半导体材料的需求,半导体材料行业迎来快速发展的黄金期。在国家鼓励半导体材料国产化的政策导向下,本土半导体材料厂商不断提升半导体产品技术水平和研发能力,逐渐打破了国外半导体厂商的垄断格局,推进中国半导体材料国产化进程,促进中国半导体材料行业的发展。
数据显示,2017-2019年中国半导体材料市场规模逐年增长,从2017年的76亿美元增长至2020年的94亿美元。据统计,2017-2020年全球62座新投产的晶圆厂中有26座来自中国大陆,占比超过40%,成为增速最快的地区。伴随着5G时代的来临,汽车电动化进程拉动IGBT规模增长。得益于对清洁能源高速增长的需求,IGBT市场规模将持续增长,IGBT市场在2020年的规模为54亿美元,从2020年到2026年将以7.5%的复合年增长率(CAGR)增长,预计2026年市场规模为84亿美元。新能源车应用作为IGBT市场规模的重要增量,2020年市场规模为为5.09亿美元,2020-2026年的复合年增长率为23%,预计2026年新能源车用IGBT市场规模为17亿美元。
随着5G、智慧物联网时代的到来,中国大陆的半导体产业得以在众多领域实现快速与全面布局,正逐步驱使全球半导体产业从韩国、中国台湾向中国大陆转移。目前,我国已经成为最大的半导体市场,并且继续保持最快的增速,预计半导体市场增长将持续带动半导体材料行业快速发展。